If you’re a lab manager or oversee laboratory equipment in a university lab or hospital, you understand how daunting it can be to purchase equipment, whether new or used equipment.
Whether upgrading to advanced lab instruments or replacing outdated models, selecting the right lab equipment requires understanding how each item will fit into your procurement system and process. You must evaluate budget, compatibility with existing systems, space requirements, use in your research and procedures, and ongoing maintenance.
When buying lab equipment, the decision involves numerous teams, suppliers, and vendors. It’s essential to consider the needs of the lab or hospital, research teams, and patients who depend on these machines for accurate, high-quality, and safe results.
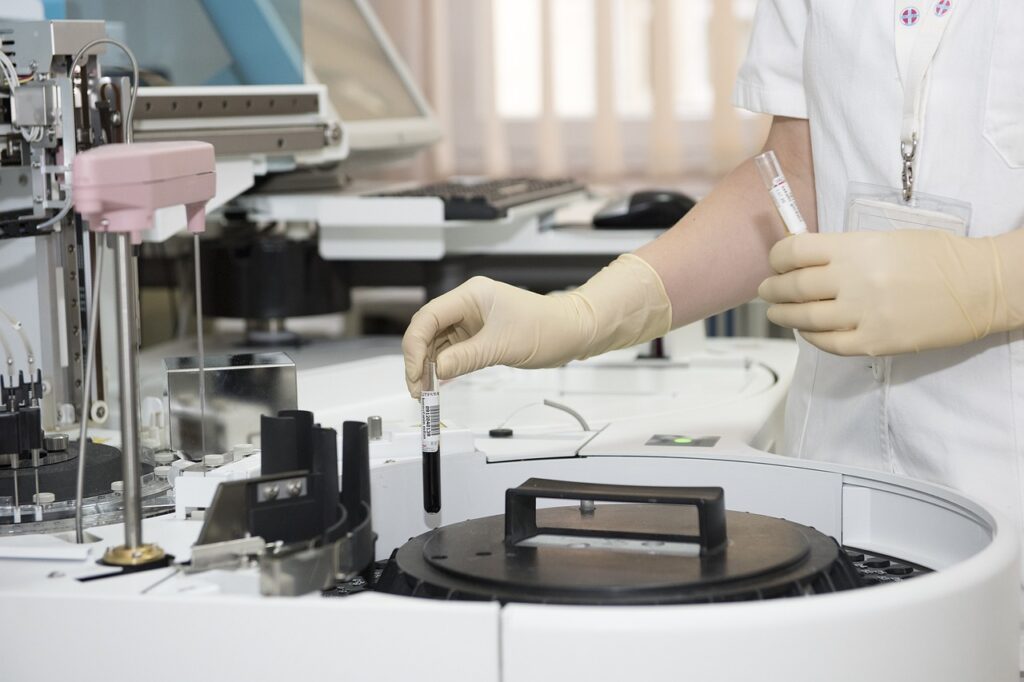
Do the benefits gained from upgrading to the most up-to-date technology provide a higher return on investment?
When buying lab equipment for research, ask yourself these questions.
- Does it make economic sense to have a portable X-ray machine?
- According to MD Buyline, a new fully-digital portable X-ray unit runs about $125,000 to $235,000 depending on maximum power output options and type of detector selected.
- Does the lab have space for a floor model centrifuge or is a tabletop model needed?
- Is it fixed or variable speed?
- Does the centrifuge need a refrigerator with or without freon?
Consider Lab Equipment Usability and Training Needs
When purchasing equipment, it’s important to identify whether a machine will require significant training. Lab equipment from different brands may have different uses, training required, and calibration needs.
Even the best research equipment may become a burden if it proves too difficult to use. Make sure training materials, ongoing support, and warranties from the manufacturer or vendors are easily accessible. This can help minimize disruptions and maximize accuracy and workflow efficiency.
Understand the Maintenance Requirements
Maintenance plays a key role in purchasing equipment. Does the vendor offer service contracts or ongoing repairs at competitive rates? Are your lab managers provided with enough training to handle the machines? What are known problems of the equipment, according to the suppliers and your own research?
Lab machines that frequently fail without covered service plans will cost most companies more in the long run. Before finalizing the lab equipment purchase, be sure to talk with your sales representative to evaluate potential vendor concerns and the availability of parts.
Assess Scalability for Future Needs
Can the new equipment adapt as your organization’s needs grow, or will you need to spend more money down the line to upgrade? Scalable lab solutions ensure you’re not re-spending on equipment prematurely.
Finally, while the initial new equipment purchase cost matters, don’t overlook associated costs like upkeep, supplies, and procurement resources. Will the lab machine save or cost more money over time? What’s the total cost compared to buying used equipment? Asking the right questions ensures you’re investing in quality equipment that will serve the company in both the short term and long term.
Proper due diligence is required before making major equipment purchases for your lab or hospital. Always shop smart, invest strategically, and ensure you’re purchasing equipment that fits your long-term goals. Let us know what other considerations are essential when you begin the procurement process. Don’t hesitate to comment below.
Next week, we will dive into budget allocation, service contracts, and the pros and cons of buying different types of lab machine parts and consumables—new versus used. Stay tuned!